This series of industrial electric furnaces is an energy-saving
industrial electric furnace made of ultra lightweight refractory
fibers. The industrial electric furnace is used in conjunction with
a temperature control cabinet. The controller can automatically or
manually control the temperature of the electric furnace, and can
be equipped with a computer meter or computer control to perform
multiple temperature measurements according to user requirements to
ensure product quality. This series of electric furnaces is a cycle
operated electric furnace. The rated temperature is 600 ℃ -1800 ℃,
used for normalizing, annealing, quenching, and other heating of
metal components in an oxidizing atmosphere.
Industrial electric furnace equipment is usually a complete set,
including the furnace body, power equipment (furnace transformers,
rectifiers, frequency converters, etc.), circuit breakers,
auxiliary electrical appliances (resistors, compensation
capacitors, etc.), vacuum equipment, detection and control
instruments (electrical instruments, thermal instruments, etc.),
automatic adjustment systems, and furnace mechanical equipment
(feeding and discharging machinery, furnace body tilting devices,
etc.).
The main components of an industrial electric furnace include:
industrial furnace masonry, industrial furnace exhaust system,
industrial furnace preheater, and industrial furnace combustion
device.
Industrial electric furnace - medium frequency electric furnace
An intermediate frequency furnace is a power supply device that
converts 50Hz AC power into intermediate frequency (from 300Hz to
1000Hz). It rectifies three-phase AC power into DC power, which is
then converted into adjustable intermediate frequency current to
supply the intermediate frequency AC current flowing through the
capacitor and induction coil. It generates high-density magnetic
field lines in the induction coil and cuts the metal material
contained in the induction coil, generating large eddy currents in
the metal material.
Due to the principle of medium frequency induction heating being
electromagnetic induction, its heat is generated within the
workpiece itself. Ordinary workers can continue working on forging
tasks in ten minutes after using a medium frequency electric
furnace, without the need for professional furnace workers to
perform furnace burning and sealing work in advance. Due to the
fast heating speed of this heating method, there is little
oxidation. The oxidation loss of medium frequency heating forgings
is only 0.5%, the oxidation loss of gas furnace heating is 2%, and
that of coal-fired furnace is 3%. The medium frequency heating
process saves materials, and each ton of forgings saves at least
20-50 kilograms of steel raw materials compared to coal-fired
furnaces. The medium frequency furnace has fast heating speed, high
production efficiency, less oxidation and decarburization, prolongs
the life of the mold, superior working environment, improves the
labor environment and company image of workers, low energy
consumption, fast melting speed, good energy-saving effect, low
burning loss, low energy consumption, self stirring function,
uniform melting temperature and metal composition, good electric
heating working environment, and good startup performance. It can
achieve 100% startup for both empty and full furnaces.
Application:
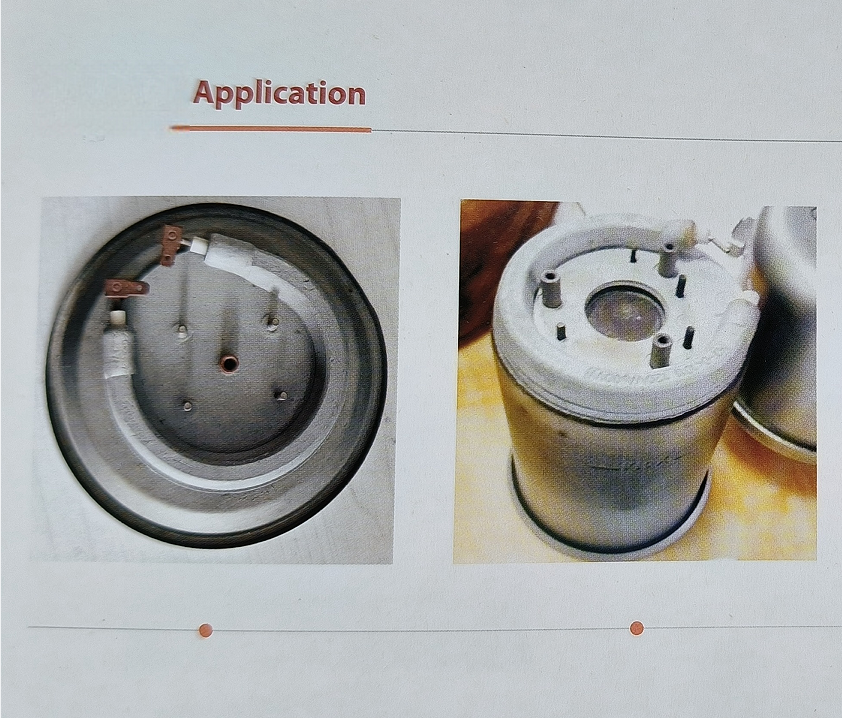
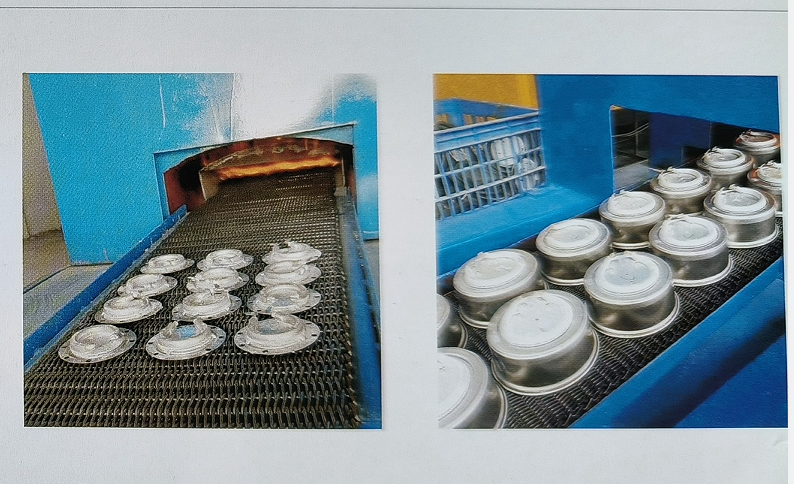
Characteristic:
●Adoptfor heat-resistance stainless steel belt or mesh belt
transmit the heat treatment workpieces to pass through heating zone
and colingzoneAndinjectinsert gas or gas ammonia decomposition as a
protective atmosphere to prevent and avoid the workpiece oxidation
in the processafheatingand cooling, to ensure the brazing surface
brightness, no oxidation, no scratches and welding line satiation
●Fumacehearth(i.e.hearting zone or muffle) adopt for imported
Sweden heat-resisting temperature nickel metal 310S) to ensure
thattheworkprietemperature come down to technical requirement when
outlet.
●Withreasonable structure ofheating, uniform furnace temperature,
workpiece on the conveyo belt running smoothly, lit deformation.
Fumaehearth sze Canbe acroding to customer's dif size of the
product and production design and manufacturing, with a strong
specificity and generality.
●Channelfurnace overall appearance is "bridge" structure, front
back inlet and outlet chamber using high quality materials into
intermediate sandwichpipe body;The front and back working face with
horizontal line to be a certain angle, the angle designis6 ' . lts
advantages to saving protectiveatmosphere consumption, reduce the
production cost.
●Adopts advanced frequency control of motor speed conveyor belt
control system, realize the stepless variable speed drive of
components, preciselycontrolthe workpiece in the running time of
the heating zoen, ensure the aluminum brazing process curve
accurate implementation.
● Equipped with modem energy saving type ammonia decomposition
funace.
Thchnical Parameters:
Specifications:
Description |
Continuous gas shielded aluminum brazing furnace equipment |
Automatic constant temperature control |
Advantage: safe operation. |
Operator: 1 person. |
Rated Power(KW) | 150 |
Rated Voltage(V) | 380x3 |
Working Temperature(℃) | 1500 |
Effective Cooling Length (MM) | 18000 |
Heating up time(h) ≤4 |
Empty furnace loss power (KW) | 45 |
Output (kg/h) | 280 |
Decomposition power (KW) | 24 |
Decomposition capacity (m ³/h) | 15 |
Heating size (L*W*H) mm | 4500x800x350
|
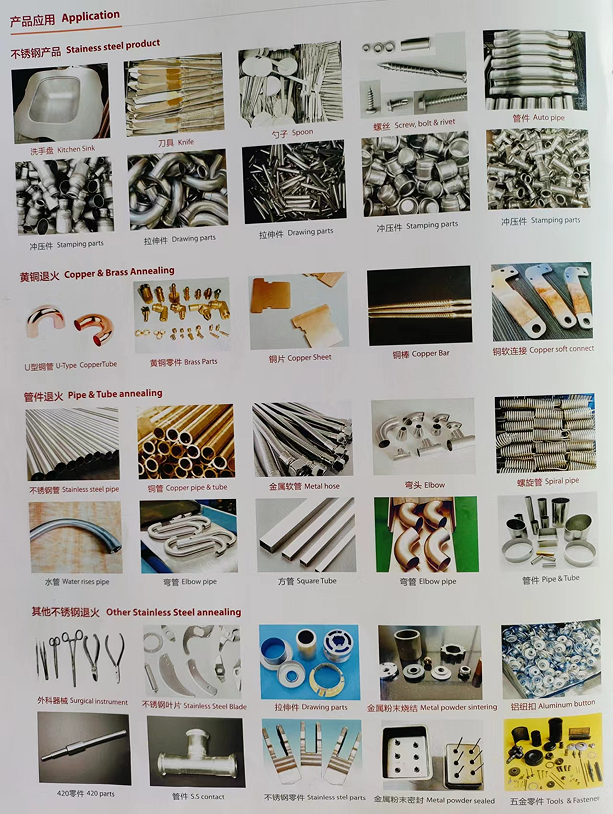