Fully Automatic Concrete Batching Plant With Dust Collecting System
Easy Operation
Parameters of Mortar Mixing Line:
Capacity | 30-80th(depending on applied formula) |
Production Circle | 3-5minutes |
Assumed Bulk Material Density | 1.4kg/m3 |
Number of Circles/Hour | 15-20(depending on applied formula) |
Sand Dosage Tolerance | ±1% |
Power Dosage Tolerance | ±1% |
Brief Descriptions of Dry Mix Mortar Plant:
The 10tph workshop type dry mortar mixer include the follwing
parts: sand bucket elevator, cement silo, screw conveyor, sand
doser, cement doser, mixer, final product storage hopper, valve bag
packer.
The premix dry mortar plant work process is as follow:
Put the classified dry sand into the inlet of bucket elevator,
hoist the sand into the sand doser, dosing the cement, put the
additives into the mixer from the additive hopper, which is onto
the mixer, after mixing, discharge the final product into the
storage silo, then flow into the packer, pack into small bags.
During the dry mortar mixer is running, the bucket elevator hoist
the sand into doser, wait for next batch. The cement screw work at
the same time.The whole system work continuously.
Features of Dry mix mortar production line:
The dry mix mortar production line is composed of the systems of
drying and screening of raw materials, mixing and dust-removing.
We can provide one-stop service from design to installation
according to our customers' specific requirement.
It features magnificent appearance, good quality, high productivity
and accurate mortar proportioning.
The dry mix mortar production line uses a centralized control
system, making the equipment easy to operate.
Main Components of Rednering Plaster Mortar Plant:
Item | Equipment | Functions |
1 | Material in-charge hopper | for charging material to bucket elevator. |
2 | Bucket elevator | Lifting materials to pre-mix silo. |
3 | Double shaft non-gravity mixer | uniform mixing of materials, special paddle sets suitable for fiber
mixing. Big double door could accelerate material discharge
uniformly, paddle sets are optional according different type
material. |
4 | Finished product silo | for storing finished material and secondary mixing of pre-packing
material. Finished product silo is available for connecting
automatic metering packer and manual discharging valve |
5 | Automatic metering packer | packing finished product by automatic weighing, high accuracy. |
6 | Pulse dust catcher: | absorb the dust during production process, mainly used for de-dust
from material in-charge hopper and packer. |
7 | Control cabinet | includes instrumentation and PLC control for controlling electrical
switch of the whole production lines. |
8 | Compressor | Produce compressed air for the whole air compressing system |
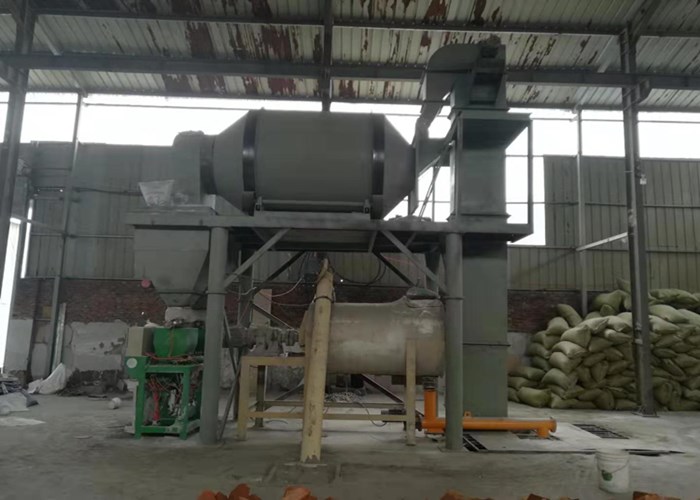